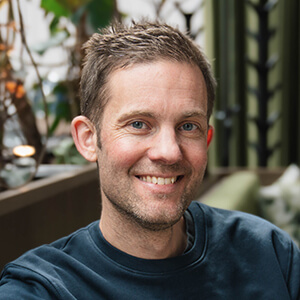
Operation: Automation
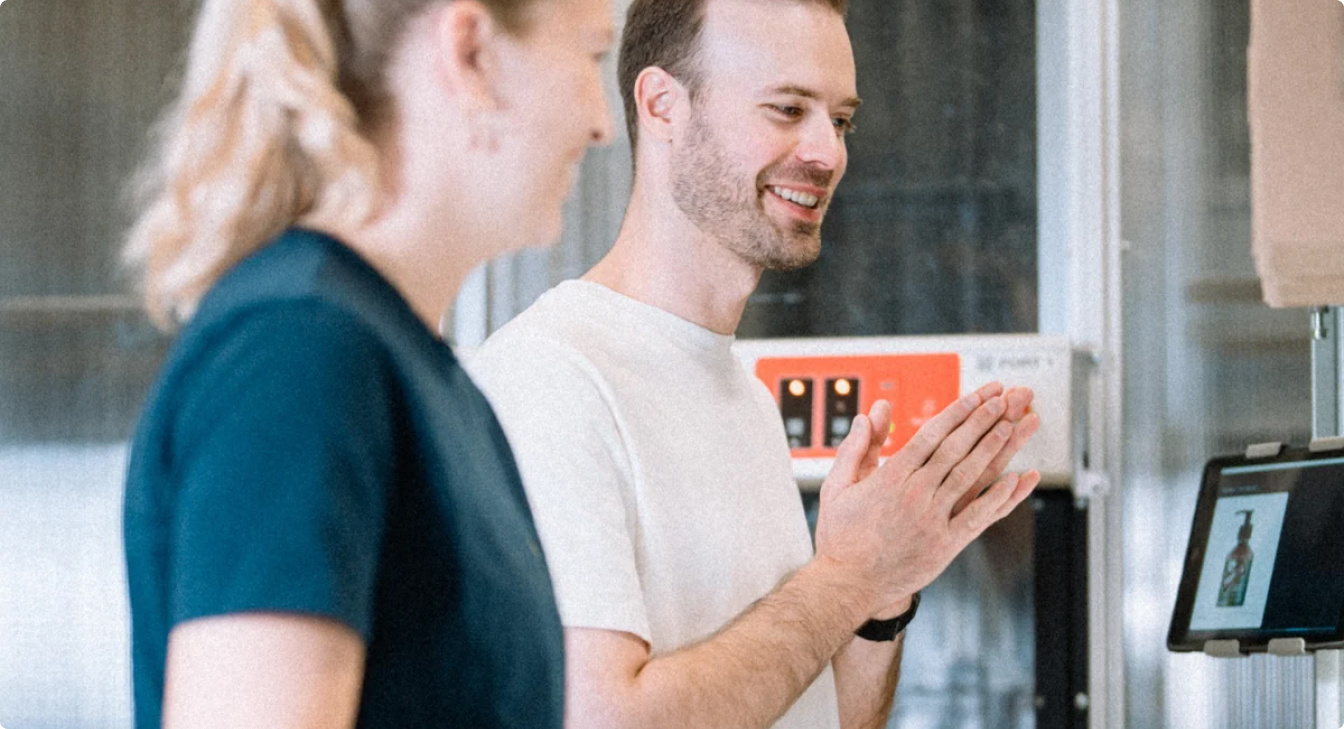
Warehouse Automation: An Introduction
AUTOMATE NOW
Ecommerce has taken off, and it’s not slowing down. If you’re not already on the ship, then you’ve long been left behind. A study from Morgan Stanley shows that ecommerce has grown to represent more than 20% of all retail sales over the last several years, and is going strong even through uncertain economic times.
Growth brings exciting potential – for instance, an influx of bold challenger brands and new small-to-midsize businesses (SMBs) all over the world. But growth also brings pain points.
As ecommerce takes over total global retail, you’ve probably noticed a parallel trend: rising consumer expectations for online shopping experiences. Accurate, reliable fulfillment gives businesses a crucial edge in a competitive landscape where customers expect their orders faster than ever. More reliable, more accurate, and faster, faster, faster… You might find yourself wondering: “How does an independent business keep up?” You’ve already leveraged digital automation tools to work smarter, not harder (e.g. Shopify, Hubspot, MailChimp, Klaviyo).
However, there’s a crucial piece missing that’s holding back your future growth, especially in efficient order fulfillment – automation of physical tasks in warehouses and fulfillment centers.
Ecommerce giants are investing increasingly heavily in warehouse automation to speed up picking, packing, sorting, and transport. Walmart is currently implementing a $14 billion investment to automate its distribution and fulfillment centers. Early adopters like Amazon are continuing to invest, declaring $1 billion towards further warehouse automation solutions.
The implications are clear: industry giants have realized that physical warehouse automation is no longer a nice-to-have, but rather a must-have for sustainable growth in the rapidly approaching future.
- Greater accuracy with reduced human error
- Greater efficiency
- Greater productivity
- Greater autonomy
- Speeds up tasks and processes
- 24/7 working capacity
- Higher throughput handling
- Maximized space use
- Reduced operational costs
- Faster order fulfillment
- Safer and better working conditions
- Higher employee satisfaction
- Long-term resilience
- Long-term scalability
- Superior customer experiences and stronger customer relationships
- Precise inventory management and control (reduced inventory loss)
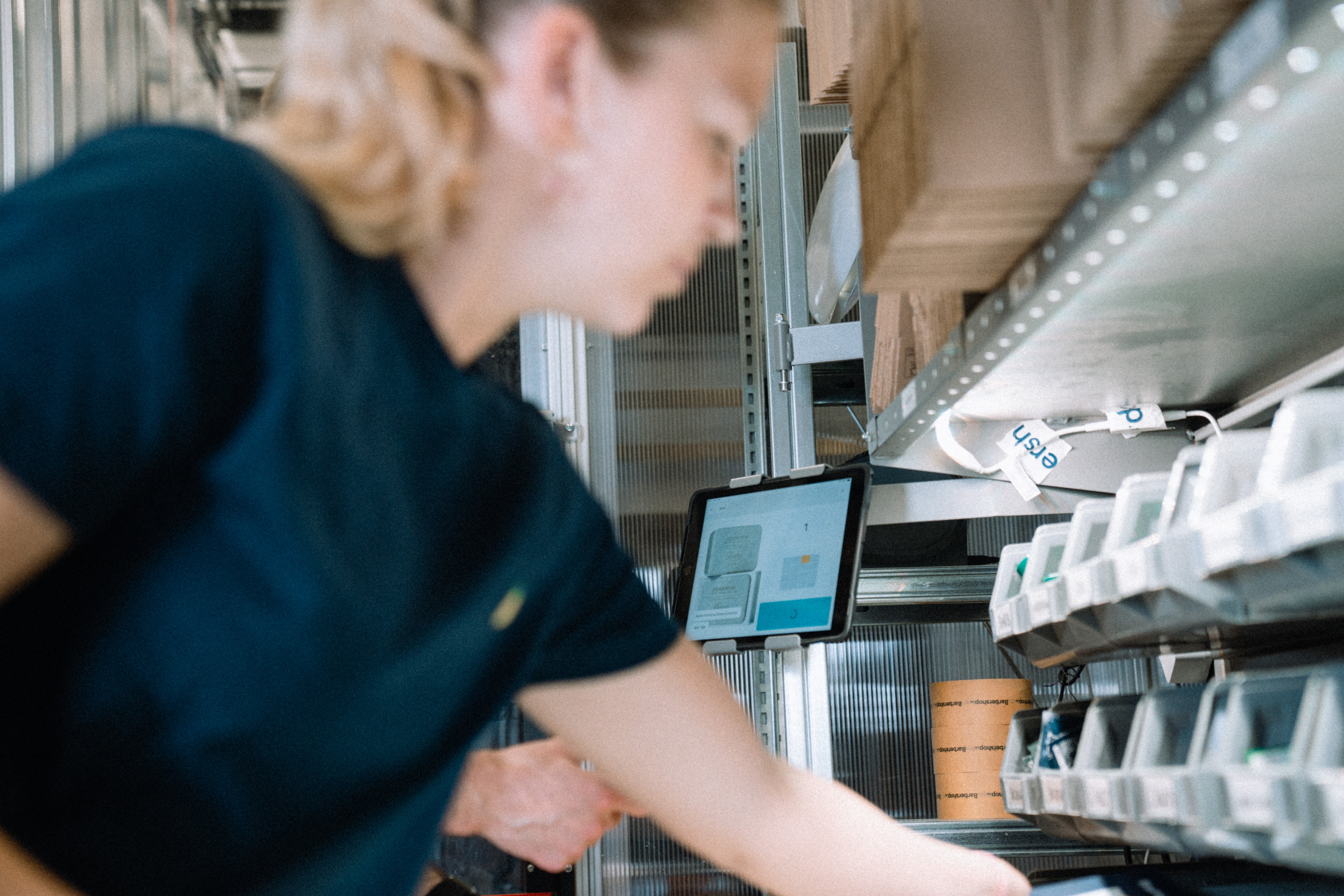
Warehouse Automation: An Overview
Historically, automated warehouse systems have required a staggering initial investment, effectively barring smaller players access to this game-changing technology. However, as our world accelerates towards automation, we believe that SMBs will need to automate – now, rather than later – for long-term resilience in an increasingly competitive ecommerce world.
THE AUTOMATION JOURNEY
Are you interested in automating your warehouse, but unsure where to start? Fear not – we’re here to guide you on your warehouse automation journey. We’ll give you a crash course on the technology and trends driving warehouse automation so that you can start making confident moves towards the best solution for your business.
- Define warehouse automation.
- Walk you through some types of warehouse automation and their pros and cons.
- Provide context and perspective for these types of warehouse automation.
- Explain how automated warehouse technology is increasingly accessible to SMBs.
- Guide you towards the best automation solution for your unique business.
- Introduce Pio – who we are, and how it works.
Warehouse Automation: A Deeper Dive
Warehouse automation uses technology to replace tedious, repetitive warehouse tasks with automated systems. Automating labor-intensive, time-consuming work (e.g. storage and retrieval) minimizes human fatigue, leaving workers free to focus on tasks with greater human value (e.g. quality control). At its core, this technology exists to enhance the flow of products in and out of warehouses - helping businesses bring their products to people more quickly, accurately, and efficiently.
Warehouse automation includes both digital and physical automation, but we’ve focused this guide on physical automation.
G2P, AMR, AGV, ASRS…it’s easy to get lost in the acronyms. So let’s break it down.
G2P refers to an innovative shift in workflow – rather than people hunting down inventory, G2P automation solutions bring goods to the person. Consider how much time is wasted walking up and down aisles, carrying heavy items, and searching shelves. When goods are brought to the person, we boost speed and accuracy while reducing labor costs and physical demand – it’s much more efficient.
ASRS: Automated Storage and Retrieval Systems
ASRS is an umbrella term for systems that automate the storage, retrieval, and management of inventory in a warehouse. Usually, ASRS replaces traditional shelving and can include shuttles, robots, and a combination of hardware and software to accelerate picking times and other warehouse processes. Prevalent and emerging warehouse automation solutions include:
- Can be easily implemented in existing warehouse structures without disrupting operations
- No need to build physical tracks or rails
- Can transport large amounts of inventory by moving entire pallets of goods
- No storage density improvements
- Limited scaling possibilities (traffic)
- No need to build physical tracks or rails
- Primary use case is to replace conveyors – less suitable for product retrieval in warehouses with high density storage
- The densest storage solution
- Minimal risk of human injury involved in product picking
- Ease of inventory management Highly scalable in performance (adding robots and ports) and capacity (adding bins and expanding grid)
- Highly modular and can be built around obstacles and space constraints
- No single point of failure means high uptime and reliable function
- Low need for specialized training for use
- Standardized bin sizes can’t always accommodate all product types
- Maximum height of 10 meters
- Business case is affected by order profile (worse ABC structure = more robots = higher investment)
- One of the fastest solutions
- Ideal for dynamic, high-volume contexts
- Able to handle various formats such as pallets, cases, cartons, bins, and totes
- Can be built to great heights for greater capacity, with multiple levels and aisles
- Minimal risk of human injury involved in product picking
- Ease of inventory management
- Requires specialized maintenance personnel on site
- Single points of failure – if a lift fails, then it reduces productivity of entire system
- Requires specialized personnel
- Requires space-consuming aisles Difficult to scale
- Various models within the ACR family can address different storage needs and products
- Can move totes and cartons of different sizes, double-deep storage, tray, and tire storage that don’t require containers
- Hybrid solution which combines strengths of various technologies
- Maximum height of 10 meters
- Need for aisles reduces storage density
Let's take a look at how the uses cases for this technology compare, between Industry Giants and SMBs.
Mobile robots were one of the first automation technologies to be implemented by industry giants such as Amazon, an early adopter of AGVs and AMRs to reduce manual labor in warehouses. However, rather than being used for storage and retrieval, mobile robots are typically used for transport from point A to point B, such as connecting storage zones with production lines – a more mobile replacement for conveyors.
Mobile robots are best used for transport, and aren’t optimized for the task of storage and retrieval. This notably limits their use case for SMBs that would benefit from a more holistic ASRS solution.
Large retailers such as Best Buy and Ikea have already adopted cube-based storage to maximize space use and create leaner teams of workers. The modular design of cube-based storage is particularly suited for businesses who seek to expand.
Cube-based storage is a compelling solution for SMBs largely due to its simplicity, flexibility, and scalability. Its ability to accommodate space constraints also fulfills common SMB needs. Cube-based storage is a particularly strong solution for businesses with a high number of unique SKUs, such as vintage fashion or resellers.
Industry giants such as Pepsi Co have implemented extensive shuttle systems for their impressive speed and ability to retrieve entire pallets of inventory. Large warehouses leverage the shuttle system’s ability to be built both multiple layers deep and extremely high. These shuttle systems are often integrated with additional automated elements such as conveyors, sortation technology, and other adjacent tech.
Shuttle systems may be suitable for SMB warehouses with a lot of usable vertical space. As the shuttle system can be built to a great height, it can maximize capacity more than other solutions with height limitations. Shuttle systems also significantly enhance the speed of product picking in SMB warehouses.
ACRs are relatively new to this space, but massive retailers such as Booktopia have already begun to implement ACR systems. This has successfully cut down on labor costs, increased storage density, and boosted speed of order fulfillment.
ACRs were developed specifically to handle caseloads of inventory, but are quite versatile, with various models suitable for various contexts. Scalable in both capacity and performance, ACRs work well to serve SMBs with lower throughput.
Warehouse Automation: For SMBs
The future of ecommerce is accelerating towards automation, with no signs of slowing down. To stay relevant, businesses of all sizes need to adapt – sooner, rather than later. Fortunately, as warehouse automation technology becomes more prominent, it’s also becoming increasingly accessible. SMBs can now take crucial steps towards automating their operations, and reap the greater efficiency, productivity, and accuracy that automation affords.
Each company is on its own unique journey, so warehouse automation solutions aren’t a one-size-fits-all.
To tailor physical warehouse automation technology to your specific needs, first evaluate your business from these 3 angles:
After you've taken a thorough look at your current operations, evaluate your automation options based on these factors:
Consider how much space you have, and might need in the future. Some automation solutions are more compact than others. If you need to maximize space, then a cube-based design provides an ultra-dense storage solution. If space isn’t an issue, a shuttle system could be right for you. Different automation systems also carry varied carbon footprints. Battery type and energy consumption are major factors in how eco-friendly a system ultimately is. As a win-win, lower energy use entails lower energy costs.
Consider initial investment only in context of eventual return on investment. Some systems may require a high upfront cost, but project a positive ROI in a matter of months or a couple years. Looking towards the long-term benefit helps build a resilient business. Most automation solutions reduce labor costs, and many reduce energy or rental costs, combining towards a rapid ROI that’s well worth the investment.
However, the time it takes to see that ROI ultimately depends on your chosen system and implementation strategy – from evaluation to design, to installation and ramping up to full performance.
System downtime equals business downtime. Look for automation systems that avoid single points of failure so that even if one element goes down, another element can work in its stead. The riskiest systems have big points of failure that block access to entire sections of inventory, and lead to frustrating order delays.
Checking a system’s proven uptime to measure its reliability is also a smart move before making your final choice.
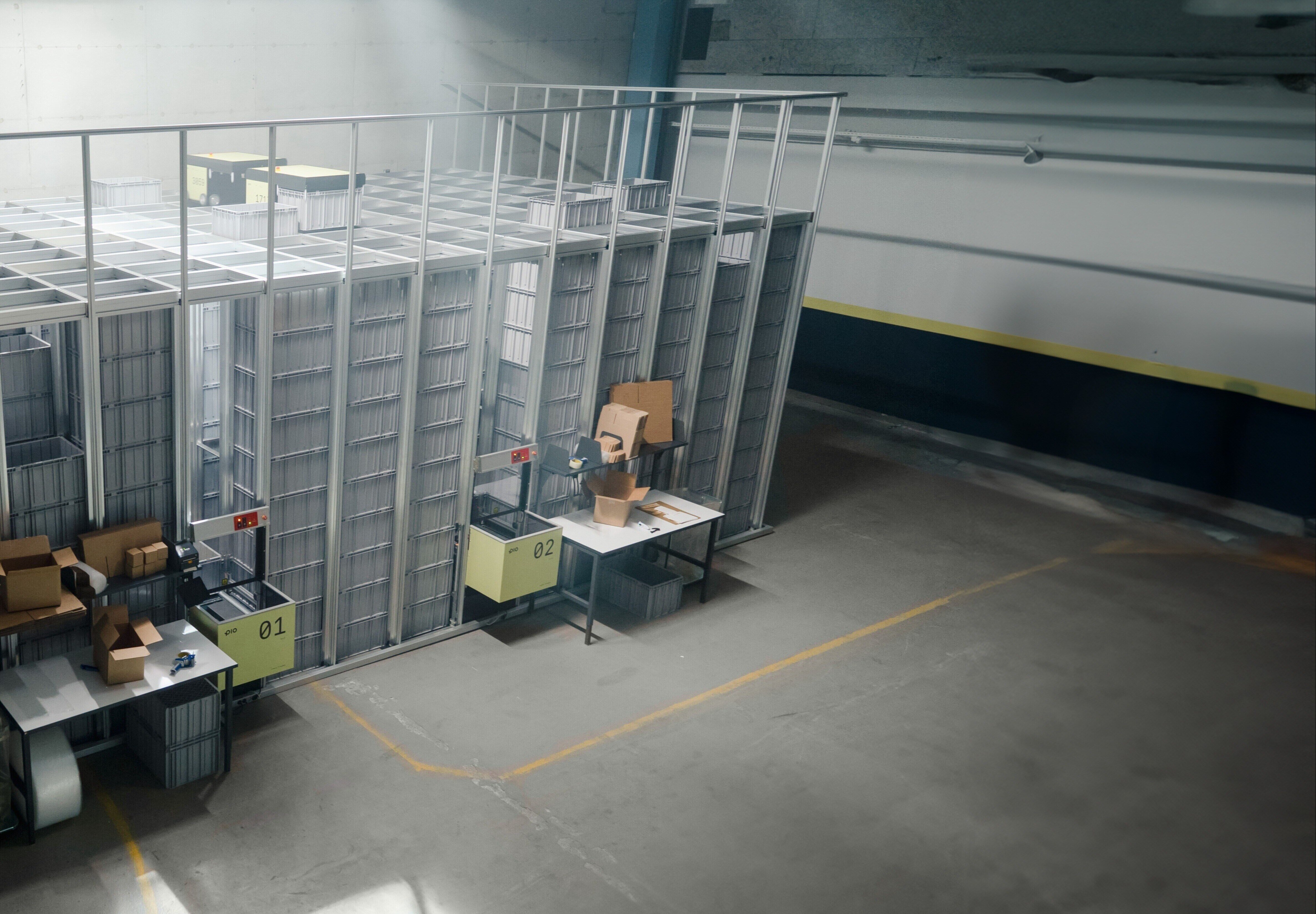
Introducing Pio
YOU’VE MADE IT THIS FAR – WE’RE SO GLAD!
Now, we’d like to introduce you to Pio: the first warehouse automation system designed specifically for small-to-midsize businesses.
Pio is a plug-and-play version of the pioneering cube-based ASRS from AutoStore, which has been developed for 25+ years. You store your inventory in Pio’s bins, that are configured to fit your product and stack closely together like building blocks in a grid (think: Rubik’s cube) to create the densest storage solution in existence.
Rather than hunting down goods in a maze of shelves and aisles, you simply tap a screen, and Pio delivers goods to access ports, faster and more accurately than a manual system. We sometimes describe Pio as a next-gen vending machine for your warehouse that makes storing and retrieving products an effortless process.
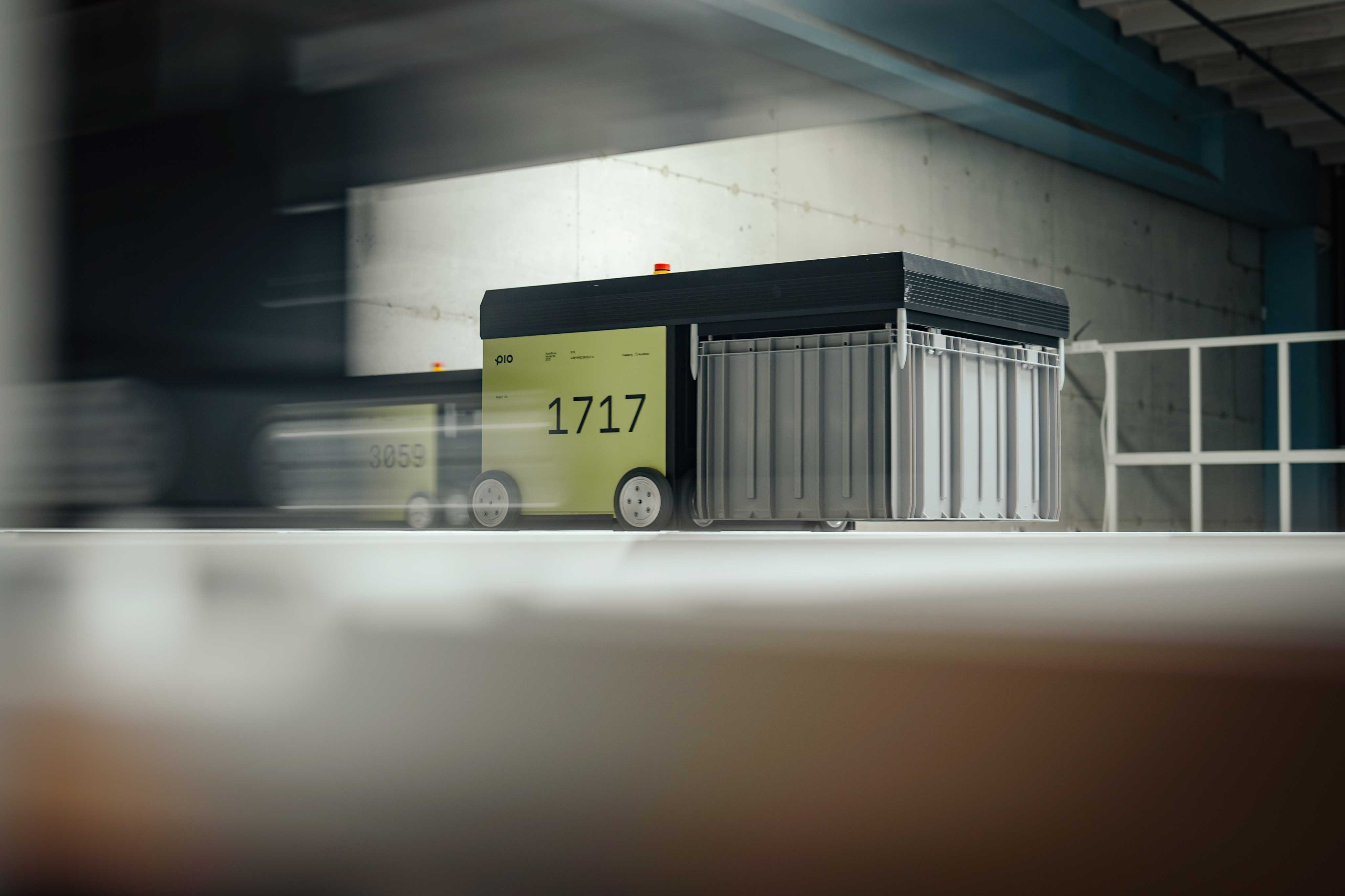
If your warehouse is dealing with picking errors, poor productivity, labor shortages, and mismanaged inventory, or you’re simply ready to make moves towards the automated future, Pio might be the perfect solution for you.
Book a free call with our team to ask questions, learn more, and discuss the best strategy for automating your warehouse, today.
Explore our resources to learn more about warehouse automation and beyond.
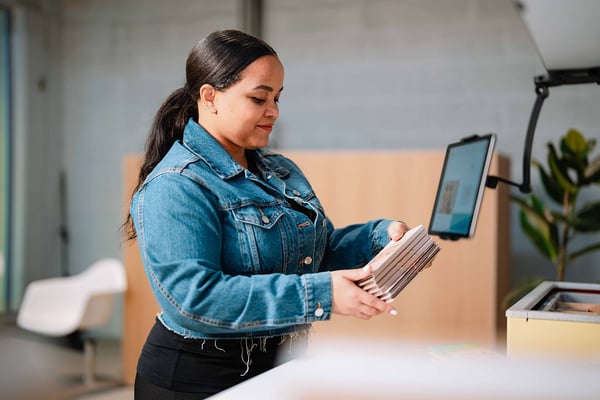