Why Space Optimization Matters
Underutilized or poorly managed warehouse space drains productivity. Cluttered aisles slow down picking times, crowded racks lead to errors, and wasted vertical space is an opportunity lost. Efficient storage is more than organization—it's about maximizing every inch of your facility to improve workflow and output.
Common Signs of Warehouse Space Inefficiency:
- Products are frequently moved to make room for incoming stock.
- Aisles feel congested, affecting picking speed.
- Overstock is stored off-site, adding logistics costs.
- Seasonal peaks overwhelm existing storage capacity.
The good news? Space constraints are often a symptom of underutilization, not a lack of square footage. Here’s how to fix that.
1. Go Vertical with Automated Storage
The Opportunity: Most warehouses severely underutilize vertical space. Tall ceilings are valuable real estate that, when leveraged correctly, can dramatically increase capacity without expanding the floor plan.
The Solution: Automated storage and retrieval systems (ASRS) allow you to use vertical space efficiently, storing products in compact, stackable bins that bots retrieve on demand. With systems like Pio, you can reduce your storage footprint by up to 90%, consolidating what previously occupied thousands of square feet into a streamlined vertical grid.
Example: One of our clients, Privada Cigar Club, compressed 3,000 square feet of inventory into just 500 square feet using the P100 (our automated warehouse system designed especially for the smallest of spaces). This freed up space for new product lines without requiring additional warehouse space.
2. Optimize Inventory Layout for Faster Access
The Opportunity: Inefficient inventory placement leads to wasted space and wasted time. High-velocity items stored far from packing stations or irregular layouts disrupt the flow of operations.
The Solution: Implement a slotting strategy—placing frequently picked items closer to packing areas and slower-moving products in less prime real estate. Reevaluate your layout every quarter to ensure your top SKUs are always within easy reach.
Pro Tip: Use software to track item velocity and reorganize layouts based on real-time data. This ensures your highest-demand products are stored for quick access, reducing wasted aisle space and unnecessary foot traffic.
3. Reduce Aisle Width with Automation
The Opportunity: Traditional manual picking requires wide aisles to accommodate forklifts and workers, resulting in wasted space that could otherwise house more inventory. Wide aisles create inefficiencies, especially in high-density warehouses where maximizing every square foot matters.
The Solution: Automated storage and retrieval systems (ASRS) and robotic picking solutions drastically reduce the need for workers to manually navigate aisles. By deploying robots to retrieve and transport products, aisle width can be cut by as much as 50%. This not only increases the amount of shelving but also improves picking accuracy and reduces errors caused by human handling.
Pro Tip: Begin by conducting a warehouse layout audit. Evaluate where aisle widths can be reduced without compromising safety regulations. For example, areas with low picker traffic can be the first candidates for automation. The upfront investment in automation can often be offset by the increased capacity and throughput gained from reclaiming valuable space.
4. Consolidate SKUs and Eliminate Dead Stock
The Opportunity: Excess stock, slow-moving SKUs, and discontinued products consume valuable space that could otherwise be allocated to faster-moving inventory. Dead stock often sits for months (or years), tying up resources and creating congestion.
The Solution: Regular SKU rationalization—auditing your product catalog for underperforming or obsolete items—frees up capacity for higher-velocity goods. Use data analytics to identify low-turnover items and liquidate or bundle them with faster-moving products. Implement just-in-time (JIT) inventory practices to prevent over-ordering and reduce unnecessary stock accumulation.
Pro Tip: Establish quarterly reviews of inventory performance and set clear KPIs for SKU turnover. Develop relationships with suppliers to enable drop-shipping for slow-moving or seasonal products, so you can store only the most in-demand items in-house. Additionally, consider creating an outlet or clearance section on your e-commerce platform to efficiently move aging stock.
Case Example: A retailer audits their SKU performance and identifies 15% of their stock as low-turnover. By bundling and liquidating these products, they reclaim 20% of their warehouse space, allowing for expansion of high-demand product lines.
5. Implement Modular and Dynamic Storage
The Opportunity: Static shelving and fixed racking systems limit adaptability, forcing warehouses to accommodate inventory within fixed layouts. This results in underutilized vertical and horizontal space, as storage doesn’t evolve alongside fluctuating inventory sizes or seasonal shifts.
The Solution: Modular shelving and dynamic storage solutions allow warehouses to adjust configurations based on product dimensions and seasonal demands. Movable racks, vertical lift modules (VLMs), and mobile shelving systems enable rapid reorganization, ensuring space is used efficiently as inventory changes.
Actionable Insight: Invest in racking systems that can easily be resized or repositioned. Implement VLMs to utilize vertical space, increasing storage capacity by as much as 80% without expanding your warehouse footprint. Movable shelving is especially useful in retail or e-commerce environments where product dimensions frequently change.
For instance: A clothing retailer shifts to mobile shelving units that can expand during peak seasons and collapse during off-seasons, increasing usable storage by 25% without expanding warehouse size.
6. Reclaim Underutilized Areas
The Opportunity: Overhead space, mezzanine levels, and areas above packing stations and walkways are often overlooked, leading to inefficient use of cubic footage. Ground-level space remains congested while upper vertical space remains untapped.
The Solution: Install mezzanines, overhead shelving, or stackable storage to utilize previously underused areas. Mezzanines can double as office space or additional storage, freeing up prime ground-level real estate for faster-moving SKUs and high-turnover goods.
Implementation Tip: Walk through your facility and identify overhead areas that could support secondary shelving or overhead conveyor systems. Consider adding vertical carousels or mezzanines above picking zones to maximize space without disrupting existing workflows.
Real-World Example: A warehouse installs a mezzanine over their packing stations, increasing their available storage by 30% and creating a dedicated zone for overflow inventory, reducing clutter on the main floor.
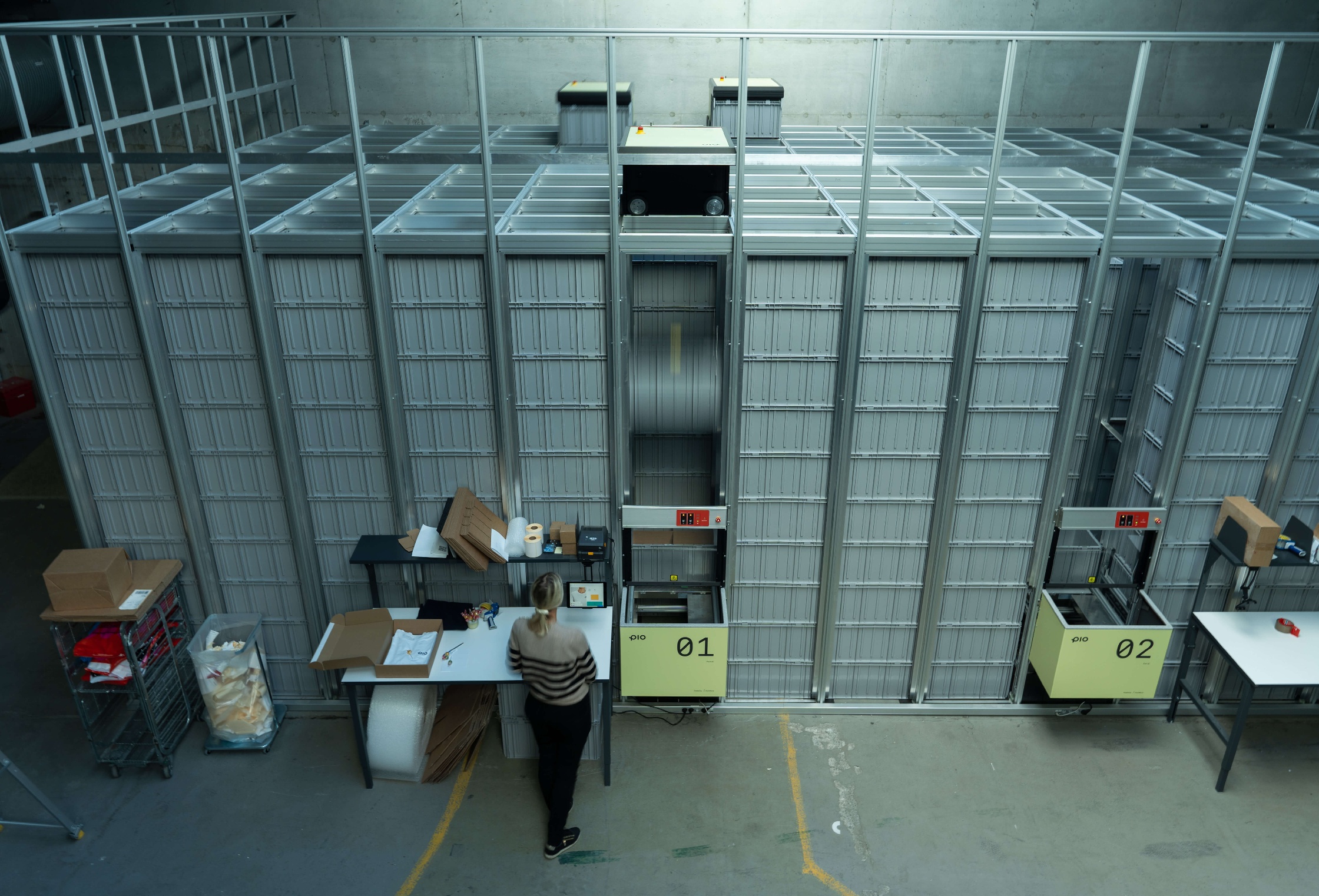
7. Reduce Picking Zones with Automated Systems
The Opportunity: Manual picking processes often require large, dedicated areas for workers to move between aisles and stations, consuming valuable warehouse space.
The Solution: By automating picking, warehouses can condense pick zones and eliminate the need for wide pathways between shelving units. Automated systems can store items more densely and retrieve them without human movement, shrinking the footprint required for order fulfillment.
For instance: A fulfillment center using automation reduces their picking area by 40%, reallocating that space to higher-density storage, enabling them to stock more products without expanding their warehouse footprint.
Thinking Smarter Can Mean Thinking Smaller
Reclaiming space in your warehouse doesn’t require moving locations or investing in costly expansions. With a few tricks and an innovative approach, you can maximize the efficiency of your existing footprint—or even shrink it.
Ready to make it happen for your warehouse? Have more questions on this topic? Let’s talk.