It has completely revolutionized processes by streamlining labor-intensive tasks such as inventory handling, order processing, and logistical processes.
The global warehouse automation market is expected to grow from $22.2 billion in 2023 to around $46.9 billion by 2028. However, for any business considering implementing warehouse automation technology, one question looms large: how much will it cost?
The truth is, the price of warehouse automation technology varies greatly based on the type of automation, the supplier, and the scale of the implementation.
In this blog, we aim to provide an understanding of how the costs associated with automating your warehouse are calculated, shedding light on the financial considerations of this technological advancement.
Factors That Influence the Cost of Warehouse Automation
Several factors influence the cost of an automated warehouse, including:
1. Type of Technology
The specific automation technologies you choose come with varying prices based on their complexity and capabilities.
Some examples of automated warehouse technology include:
- Automated guided vehicles (AGVs): AGVs are mobile robots that navigate and move materials within a warehouse. They can transport goods, pallets, or containers and follow predefined paths or routes.
- Robotic picking systems: Robots are used for picking and packing tasks. They can handle various products and collaborate autonomously with human workers.
- Automated Storage and Retrieval Systems (AS/RS): AS/RS systems use automated machines and software to manage and organize inventory within a warehouse. This warehouse automation solution can efficiently store and retrieve goods from designated storage locations.
- Conveyors and sortation systems: Conveyors transport items within a warehouse. Sortation systems automatically sort products based on criteria like destination, size, or weight.
- Shuttles and goods-to-person systems: Shuttles are automated devices that move within storage racks to retrieve and transport goods to a picking station. Goods-to-person systems bring products to warehouse workers for picking instead of them traveling to the products.
- Automated packaging systems: Automated machines can pack products into boxes, apply labels, and prepare items for shipping. This includes case erectors, case sealers, labeling machines, and more.
- Warehouse Management Systems (WMS): A Warehouse Management System is a software application that optimizes and orchestrates the flow of work and inventory within a warehouse. It helps coordinate and manage various automated and manual labor tasks.
- Pick-to-light and put-to-light systems: These systems use lights and displays to guide workers in picking and placing items accurately and efficiently.
- Inventory management systems: Advanced software and systems that use real-time data to track and manage inventory, helping optimize stock levels and reduce overstock or stock-outs within the supply chain.
- Robotic forklifts and material handling equipment: Robots can handle pallets and heavy loads, assisting with loading, unloading, and moving materials within automated warehouses.
2. Level of Automation
The extent to which you automate processes in your warehouse significantly impacts costs. Basic automation tends to be less expensive than advanced robotic automation.
Automated warehouse systems can be sorted into three categories:
- Low-level automation: Basic automation like conveyor belts, barcode scanners, and simple inventory management systems may start at around $10,000 to $50,000.
- Mid-level automation: Incorporating technologies like automated storage and retrieval systems (AS/RS), automated sortation systems, or robotic assistance could range from $70,000 to $1 million+, depending on complexity.
- High-level automation: Advanced automation involving highly sophisticated robotic systems, fully integrated warehouse management systems (WMS), and goods-to-person (G2P) systems can range from $500,000 to several million dollars.
3. Warehouse Size and Layout
The size of your warehouse and its layout will influence the type and amount of automation required. Larger warehouses might need more automation components, impacting the overall cost.
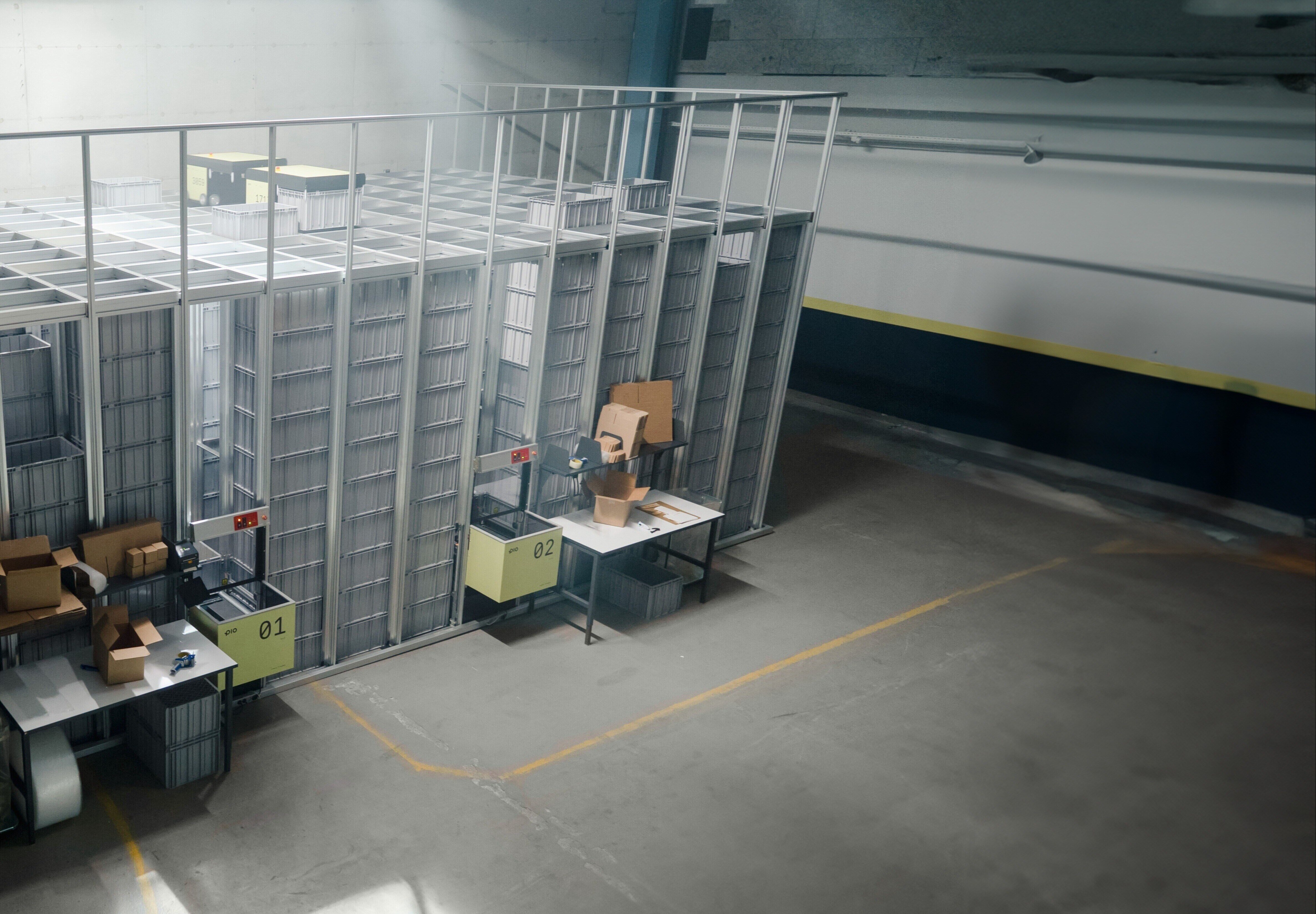
4. Customization and Integration
Tailoring automation solutions to meet your warehouse's specific needs often involves additional costs. Integrating existing systems and customization to fit your operations can increase the overall price.
5. Supplier and Brand
Different suppliers and brands have their pricing structures. Established and reputable suppliers might have higher upfront costs but could offer better long-term support and reliability.
6. Scalability and Future Expansion
Considering future growth and the ability to scale the automation system is essential. Investing in a system that can easily adapt to your future needs can affect the initial cost.
7. Complexity of Operations
The complexity of your warehouse operations, including the variety of products, order volume, and the intricacy of order fulfillment processes, will influence the automation components required and, consequently, the cost.
8. Maintenance and Support Costs
Factoring in ongoing maintenance, repairs, and support services is crucial. The complexity of the automation system may impact these costs over time.
9. Training and Workforce Costs
Training your workforce to use and maintain the automated systems can be a significant cost. Ensure you budget for training and potential changes in workforce needs.
10. Regulatory and Compliance Requirements
Compliance with industry regulations and safety standards may necessitate specific automation features or additional safety measures, affecting overall costs.
11. Return on Investment (ROI) Expectations
Consider the ROI you expect from automation. Balancing the initial cost with the long-term benefits and ROI is crucial in determining the feasibility of the investment.
Working with automation vendors or consultants who can provide detailed assessments and cost estimates based on your specific needs and circumstances is essential.
Key Takeaway
The cost of automating a warehouse can vary widely based on several factors, including the level of automation, the size of the warehouse, and the type of technology. Generally, the cost can be anywhere from thousands to millions of dollars.
When it comes to implementing warehouse automation solutions, it's important to thoroughly analyze your warehouse requirements, operational needs, and budget constraints to determine the most suitable level of automation for your business.
Additionally, consider the long-term benefits and cost savings a warehouse automation system can offer regarding increased efficiency, accuracy, productivity, and labor costs. Consulting with automation experts and suppliers can also provide a more precise estimate tailored to your situation.
Explore the Future of Warehouse Efficiency with Pio
Our innovative 'cube' storage approach strategically optimizes your inventory layout, achieving remarkable storage density that can increase your warehouse capacity by up to tenfold.
Imagine a system that efficiently stores your inventory and autonomously navigates, selects, and delivers items directly to your workstation. Pio's advanced technology transforms this vision into a reality.
With Pio, you can experience:
- An impressive 80% reduction in labor requirements
- A remarkable 99.7% system uptime
- A significant 90% reduction in required space
Pio's warehouse automation cost varies based on your warehouse's size, scope, and unique requirements.
Ready to revolutionize your warehouse operations? Delve deeper into Pio's automated warehouse system and get a detailed price quote by scheduling a complimentary strategy call with one of our experts today.