However, despite their many advantages, warehouse automation solutions are not without their challenges.
In this blog, we'll examine the challenges of warehouse automation and share practical solutions for overcoming these obstacles.
We'll also explore the great advantages of automated warehouses and take a look at common examples of automated technology in action.
The Challenges of Warehouse Automation (and Their Solutions)
As we now know, automated warehouse technology is not without its hurdles. Let's explore these obstacles and their effective solutions.
Challenge 1: Threat to Human roles
One of the primary concerns with warehouse automation is the perceived threat to human jobs. The fear of job replacement can create a sense of resistance among employees as they fear they may lose their jobs.
Solution
The key to overcoming this challenge lies in human-machine collaboration. Instead of replacing your workers, automation should be viewed as a tool that enhances their roles.
Offering upskilling and reskilling opportunities can empower employees to work alongside warehouse automation systems effectively.
Encourage a culture of continuous learning to make the transition smoother.
Challenge 2: Initial investment costs
Implementing warehouse automation technology can be a significant financial commitment, which may make you anxious about taking the leap.
Solution
The truth is that while there's no denying the initial costs can be daunting, the long-term benefits of warehouse automation speak for themselves.
We recommend calculating the Return on Investment (ROI) and considering factors like labor savings, reduced errors, and increased efficiency when making decisions.
Additionally, financing options and incentives are available for businesses investing in automation.
By carefully analyzing costs and benefits, your initial investment becomes a strategic move toward future success.
Challenge 3: Integration with existing systems
Integrating automation with existing warehouse systems can be a complex and potentially disruptive process.
Solution
Although implementing warehouse automation may seem complex, you can enjoy a successful integration experience with the correct planning and preparation.
The trick is to ensure you clearly understand your current systems and the compatibility of automation solutions. Work closely with automation providers who offer seamless integration services.
Minimize disruptions by conducting thorough testing and gradually implementing automation into your existing workflow.
Challenge 4: Maintenance and downtime
Automated systems, like any machinery, require regular maintenance, and unexpected downtime can disrupt operations.
Solution
Establish a proactive maintenance schedule to keep automation equipment in optimal condition. Schedule maintenance during off-peak hours to minimize disruptions.
Investing in robust, high-quality automation solutions that are less prone to breakdowns is also good. Consider redundancy in critical systems to ensure continuity in case of unexpected downtime.
Challenge 5: Scalability
Adapting automation systems to accommodate growth or downsizing can be challenging as your business needs change.
Solution
Plan for scalability from the outset. This includes choosing modular automation solutions that can be easily expanded or reduced.
Collaborate with automation providers who offer flexibility in scaling their systems. Don't forget to regularly assess your business's growth and adjust your automation strategy accordingly.
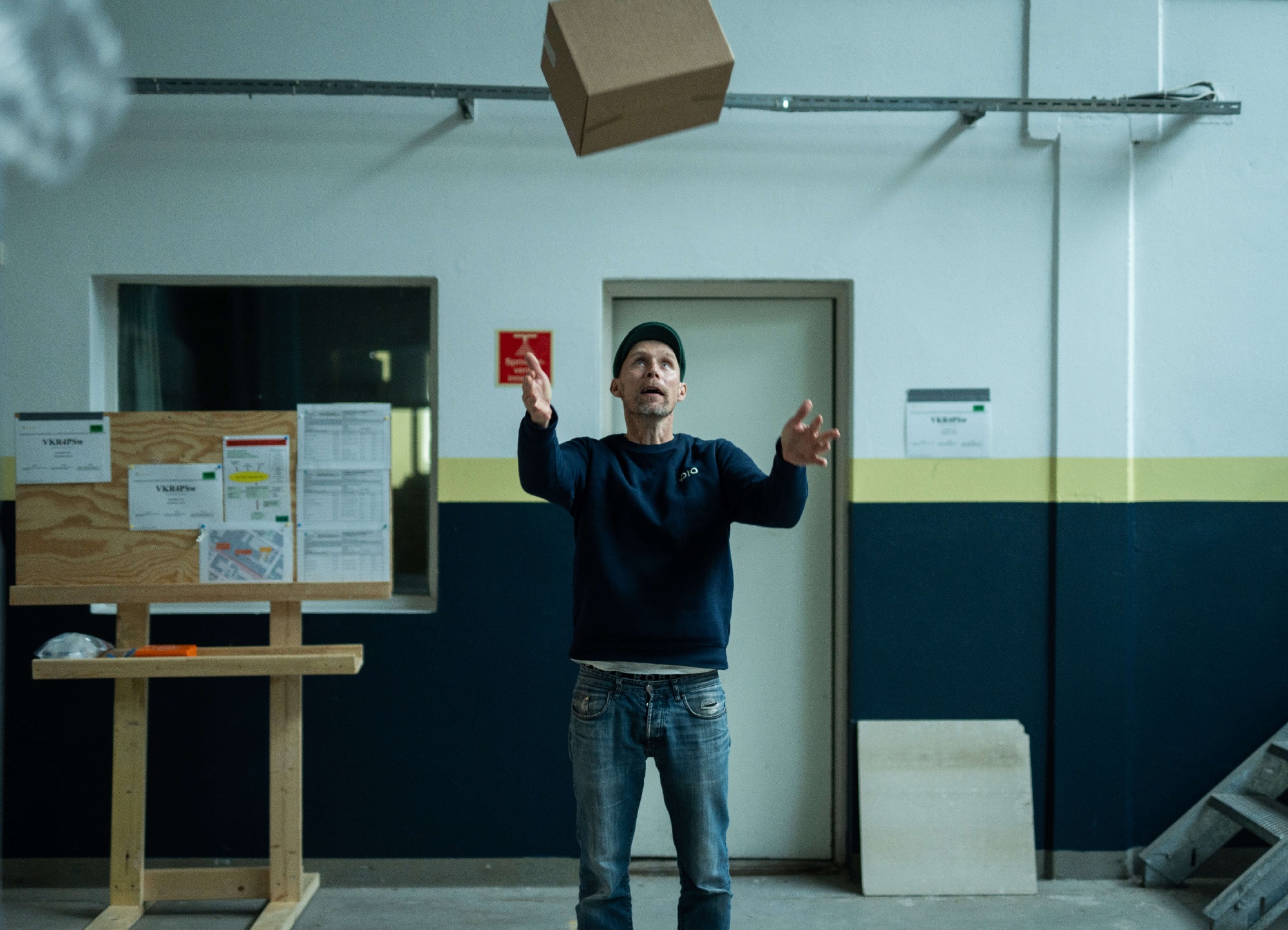
Benefits of Warehouse Automation
Warehouse automation offers numerous benefits to businesses across various industries. Here are some key advantages:
- Increased efficiency: Automation reduces manual labor and streamlines warehouse operations. Automated systems can work 24/7, improving your order fulfillment speed and accuracy. This leads to higher productivity and reduced labor costs.
- Enhanced accuracy: Automation minimizes the risk of human errors, such as picking the wrong items or incorrect inventory counts. This improves inventory accuracy and order fulfillment, reducing costly mistakes and unsatisfied customers.
- Cost savings: Reduced labor costs, fewer errors, and optimized inventory management all contribute to a more cost-effective operation.
- Inventory optimization: Automation systems can track inventory levels in real time, helping you maintain optimal stock levels. This reduces excess inventory costs and stockouts, ultimately improving cash flow and customer satisfaction.
- Safety improvements: By automating potentially hazardous tasks, warehouse automation reduces the risk of workplace accidents and injuries. This fosters a safer working environment for employees.
- Data insights: Automation generates valuable data on warehouse operations, helping you make informed decisions. Analyzing this data can lead to further optimizations, better demand forecasting, and improved overall performance.
- Competitive advantage: Companies that adopt warehouse automation gain a competitive edge. Faster order fulfillment, higher accuracy, and lower costs can attract and retain customers, helping you thrive in a competitive market.
- Sustainability: Warehouse automation can reduce energy consumption and waste, contributing to environmental sustainability. Efficient routing of goods and optimized inventory management minimize the carbon footprint of your warehouse operations.
Examples of Warehouse Automation Technology
Some common types of warehouse automation include:
- AGVs (Automated Guided Vehicles): Self-driving robots for material transport
- Conveyor systems: Automated systems for moving goods within a warehouse
- AS/RS (Automated Storage and Retrieval Systems): Robotic systems for storing and retrieving items.
- Goods-to-person systems (G2P): Automated delivery of items to workers.
- Robotics: Robots, including autonomous mobile robots, help with warehouse processes, including picking and packing.
- Sortation systems: Automated sorting and routing of items.
- Voice and pick-to-light systems: Technologies guiding pickers during the picking process.
- WMS (Warehouse Management Systems): Software for warehouse optimization.
- Automated Packaging Systems: Machinery for automating packaging.
- Drones: Used for inventory management and monitoring.
- IoT Sensors: Sensors for environmental monitoring.
- Automated forklifts: Self-driving forklifts for material handling.
- Automated palletizers: Machines for stacking pallets.
As explored in this blog, each challenge of automated technology has a practical solution to pave the way for a smoother transition into automated warehousing.
From addressing employee concerns about job displacement through human-machine collaboration to managing the initial investment costs by calculating long-term benefits, there are clear strategies to navigate these obstacles.
Ultimately, the benefits of an automated warehouse are too significant to ignore. Enhanced efficiency, accuracy, cost savings, scalability, and improved safety are just a few rewards that await those who embrace automation.
And when it comes to choosing the right technology for your warehouse, you’re spoilt for choice with many options available, including AS/RS, robotics, and drones.
Automate Your Warehouse with Pio
Introducing Pio—an Automated Storage and Retrieval System (AS/RS) designed with a grid framework but with a unique twist.
Pio employs a 'cube' storage method, strategically optimizing your inventory storage layout, resulting in an impressive storage density and up to a ten-fold increase in warehouse space.
This is a system that not only stores your inventory efficiently but also independently navigates, selects, and delivers items directly to your workstation.
Pio is designed to reduce many of the usual headaches associated with warehousing. By eliminating specific manual tasks and optimizing the rest, Pio allows you to pick and pack around 360 order lines per hour with 99.9% accuracy.
To learn more about Pio's automated storage system, you can schedule a free strategy call with a team member to get advice from our efficiency experts.