Robots vs. Human Workers: Common Misconceptions
Fear of robots “taking jobs” usually stems from the misconception that machines simply replace manual labor one-to-one. In reality, automation in warehouses is designed to complement human workers by taking over the dull, repetitive, and physically straining tasks so that people can focus on higher-value work. In other words: robots handle the mundane or dangerous duties while humans remain employed in new, often better roles.
After all, why shouldn’t robots take over the tasks that people don’t need (or want) to do?
In a traditional warehouse, workers might walk miles a day fetching items and hauling heavy bins. Robots can relieve that burden: automated systems retrieve products and bring them to a workstation, or handle tedious pallet stacking, reducing physical strain on human staff. Rather than hustling to pull orders, an associate can oversee several robot pick stations or focus on quality control, packing, and exception handling—tasks that require human judgment and dexterity.
The result is a safer, more efficient workflow where robots and people each do what they’re best at. Employees are freed from back-breaking routines and excessive overtime, which improves morale and reduces injuries. Meanwhile, orders get out the door faster and with fewer errors. It’s a win-win scenario: robots excel at speed and consistency, while humans excel at problem-solving, customer service, and adapting to changes.
Another common misconception is that employees will struggle to adapt to high-tech tools. In practice, modern warehouse automation is increasingly user-friendly. Training often takes days, not weeks, dispelling fears that only engineers can work with the bots. Brian Desind, founder of Privada Cigar Club, was impressed by how fast his team picked up on using their new Pio system: “My team learned how to work with the robots in minutes. It couldn’t be easier.”
When technology is designed with workers in mind, adoption becomes a smooth process. Instead of resisting automation, teams often welcome it once they realize it makes their jobs less tedious. Rather than making human labor obsolete, robots become helpful coworkers on the warehouse floor. In smart warehouses, humans remain integral—they’re just doing higher-value work with the robot muscle handling the heavy lifting.
Success Stories: Humans and Robots Thriving Together
Nothing dispels the “robots vs. jobs” myth better than real-world examples. Across industries in diverse corners of the world, SMBs and independent 3PLs are proving that automation can enhance human roles and even create better jobs. Let’s look at a few success stories from Pio’s customers and how their warehouse robots have amplified their human teams’ productivity, morale, and growth.
Souko Fulfillment (Salt Lake City, UT)
Souko is a fast-growing third-party logistics (3PL) provider that started in a garage and now runs a 40,000 sq. ft. warehouse. As orders surged, Souko’s founder, Connor MacArthur, knew they needed to automate repetitive processes to keep scaling. They turned to Pio’s plug-and-play robotic system – and saw transformative results. Order picking sped up to triple the rate—from about 60–80 items/hour to as high as 240–285 lines per hour per worker. In fact, the same volume of orders can now be fulfilled with half the picking labor they used before.
This doesn’t mean they laid off half their team; instead, it freed up staff to handle more clients and focus on tasks like packing and customer service. Accuracy also jumped to near-perfect levels, thanks to robots and software eliminating manual errors.
Perhaps most impressively, Souko could absorb peak season demand without burnout. During Black Friday, they pre-loaded inventory into the automated grid, which minimized frantic restocking and let their employees concentrate on packing and shipping out orders on time. Team members report less walking and fatigue and greater job satisfaction now that “the robots” fetch items for them.
Souko even found unexpected perks —the Pio system’s dashboard gamifies productivity, sparking friendly competition among workers (one star picker proudly hits 285 picks/hour, ranking at the top globally).
With robots tackling the drudge work, Souko’s people can shine at what humans do best: problem-solving and delighting customers. The company continues to hire as it grows, and notably, they no longer have to uproot to a bigger warehouse each year—the automated system expanded their storage capacity within the same footprint, so the team can grow in place without disruption.
Souko’s story shows how the business scales up and employees benefit, hand in hand.
Ko:Ko (Fosnavåg, Norway)
Ko:Ko is a family-run online apparel boutique known for vibrant women’s fashion. Founders Stine Goksøyr and Øyvind Rekkedal prided themselves on efficient operations, but as a small team they often spent entire days picking orders. Automation seemed out of reach for a “mom-and-pop” shop until they discovered Pio. Once they deployed a Pio system, Ko:Ko’s warehouse went from well-organized to perfectly efficient.
Robots now handle all the heavy lifting by retrieving products and bringing them to a packing station at the tap of a tablet. The impact on Ko:Ko’s workflow was dramatic: order fulfillment became 5 times faster, and they slashed the manual labor needed by about 80%. Øyvind notes that “before Pio, we would’ve had two people picking all day. Now there’s just one person doing it, and they’re usually done by lunch.”
This freed up one of their staff to do other important work (or simply not have to hire a second picker in the first place). It also means same-day shipping is now routine for Ko:Ko, an Amazon-level speed that wins them happy customers.
Most importantly, automation gave these owners their life back: instead of spending their days trekking through warehouse aisles, they have time to trek through the wilderness that surrounds them. Plus, they can focus on higher-value activities like designing new collections, marketing, and personalizing customer experience.
Ko:Ko’s team leverages the time savings to add those special touches their brand is known for, reinforcing their boutique’s quality and service. And on a personal level, Stine and Øyvind now enjoy well-earned breaks–they joke that with picking done by lunchtime, they’re free to relax at their seaside cabin in the afternoons.
Their experience showcases how automation and jobs can coexist: the robots accelerated the tedious parts of the job, empowering the humans to excel creatively and even improve their work-life balance.
Privada Cigar Club (Orlando, FL)
Privada Cigar Club is a specialty ecommerce retailer offering rare and boutique cigars through a subscription model. This relatively young company faced the challenge of meeting high customer demand with a lean team. By adopting Pio’s automated storage and retrieval system, Privada transformed its fulfillment operations without heavy hiring. As founder Brian Desind reports, “with Pio, we’re able to compete with the giants.”
This meant Privada could handle much larger volumes of inventory and orders in the same small warehouse space – the Pio system provided 10x more storage capacity within their existing footprint, leveling the playing field with far bigger competitors. Rather than stretching his staff thin, Desind saw the robots do the grunt work while his team ensured quality and customer engagement. Training was a non-issue: the whole team adapted quickly to the intuitive system.
With automation, Privada’s crew spends less time hunting for products on shelves and more time curating new cigar selections and interacting with their passionate customer base. The business has been able to scale up rapidly —and even as efficiency soared, no jobs were lost. On the contrary, Privada’s growth with robotics has it hiring in areas like marketing and customer support, enabled by the cost savings and productivity gains in the warehouse.
It’s a compelling example of how a small business can leverage robots to grow and create jobs, not cut them.
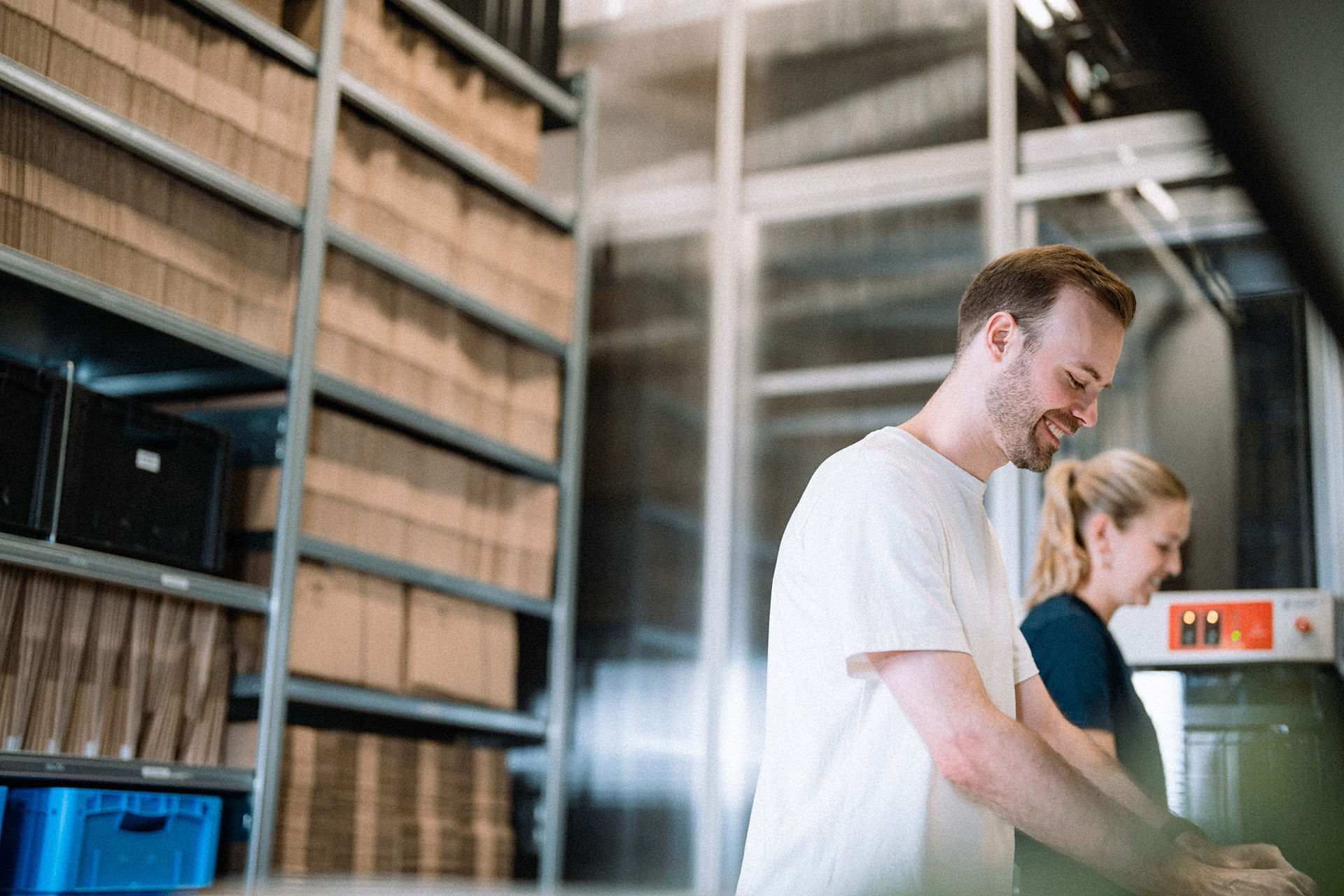
The Future of Human Work with Automation
These three Pio success stories share a common thread: in each, robots took over repetitive physical tasks, and the human workers shifted to more productive, engaging roles. The businesses achieved leaps in throughput, accuracy, and capacity—fueling expansion, which often leads to more hiring to support the growth. Employees, meanwhile, experienced less strain and more interesting work. Automation became a tool that amplified human potential.
In warehouses from apparel to electronics, that sentiment rings true – when robots handle the chores, humans can invest their energy in customer relationships, creativity, and strategic tasks that drive the business forward.
What does the future of work look like in an automated warehouse? If the trends and stories above are any indication, it’s a future where human workers are more essential than ever—but in different ways than in the past. Instead of being laborers fetching and lifting, warehouse staff evolve into operators, problem-solvers, and innovators who work alongside robotic helpers.
In a tech-driven warehouse, you might see a scene like this: Autonomous robots zip around bringing inventory totes to ergonomic stations where people stand ready to pick or pack orders. No longer racing around, workers are comfortably stationed at a workbench, managing multiple orders at once as goods-to-person robots present them with the next item. If something is misplaced or a machine needs attention, a human troubleshooter steps in to fix the issue. Far from being replaced, the employees become conductors of an automated orchestra—monitoring systems, addressing exceptions, and optimizing processes. They may use tablets or screens (as easy as a smartphone app) to control the robots or to ensure inventory data is accurate.
The skill set for warehouse workers shifts toward technology fluency and workflow management, and companies invest in upskilling their staff accordingly. This creates more engaging career paths: an entry-level picker can grow into a robotics technician, inventory analyst, or automation supervisor, rather than facing a dead-end, physically taxing job.
Crucially, humans in automated warehouses get to focus on what humans excel at. With robots handling repetitive tasks, workers can dedicate time to higher-value activities: ensuring orders meet quality standards, customizing packages, managing inbound/outbound scheduling, or developing new process improvements. They can also spend more time supporting customers’ needs (for instance, handling special requests or coordinating with sales teams)—things that directly add value to the business.
The warehouse worker of the future might have a title like “robotics operations coordinator” or “inventory optimization specialist” instead of “picker” or “forklift driver.” Their work environment will likely be cleaner, safer, and more collaborative. Collaborative robots (or “cobots”) are designed to work safely alongside people —for example, autonomous carts that follow workers to collect items, or robotic arms that assist in packing. These technologies are being built with safety sensors and intelligent programming to avoid accidents, meaning the warehouse can be a place where humans and machines work side by side in harmony.
Finally, it’s worth reemphasizing how automation improves working conditions. Fewer injuries from heavy lifting, reduced fatigue from walking 10+ miles a day, and elimination of mind-numbing tasks all contribute to a more satisfied workforce. When robots handle the drudgery, human jobs become more about supervising and fine-tuning, which tends to be less stressful and more rewarding.
Employees often feel proud to work in a forward-looking, high-tech environment. Companies have found that adding robots made their warehouse jobs more desirable and helped reduce turnover, because the work became less physically punishing. Team members at Souko or Privada are glad to have the robots around because it makes their day-to-day work easier and the company’s success more attainable.
Embracing robotics creates a virtuous cycle—happier, more skilled workers, leading to higher productivity and business growth, which then creates more advancement opportunities for those workers.
Conclusion: Embracing Robots for a Smarter, More Human-Centric Warehouse
Automation and jobs don’t have to be at odds. As we’ve seen, robots can be the key to unlocking human potential rather than a threat to it. Warehouses that integrate robots intelligently are discovering that they can achieve dramatic gains in efficiency and accuracy while also enhancing the roles of their employees. Businesses from family-run boutiques to 3PL startups are scaling up with automation by empowering their teams to work smarter. The robots handle the heavy lifting, literally and figuratively, which allows people to focus on what humans do best: creative problem-solving, improving the customer experience, and driving the business forward.
In this light, warehouse robots aren’t job-takers—they’re job-enablers and productivity amplifiers. They help companies meet growing demand and remain competitive, which in turn keeps those companies healthy and hiring. They reduce the physical toll on workers, making warehouse careers more sustainable and attractive. And they free up human workers’ time, so each person can contribute more meaningfully to the company’s goals.
The takeaway for warehouse operators and business owners is clear: embracing robotics is the path to a smarter, more human-centric warehouse. By adopting technologies like Pio, even smaller companies can create an environment where employees are safer, more engaged, and more productive than ever.
Automation doesn't replace—it elevates your workforce and your entire operation. The companies that recognize this and act on it will not only assuage the fears around robots and jobs; they’ll build thriving businesses where both people and robots are busy accomplishing bigger and better things together.
In the end, robots amplify human goals—and with the right approach, everyone wins.
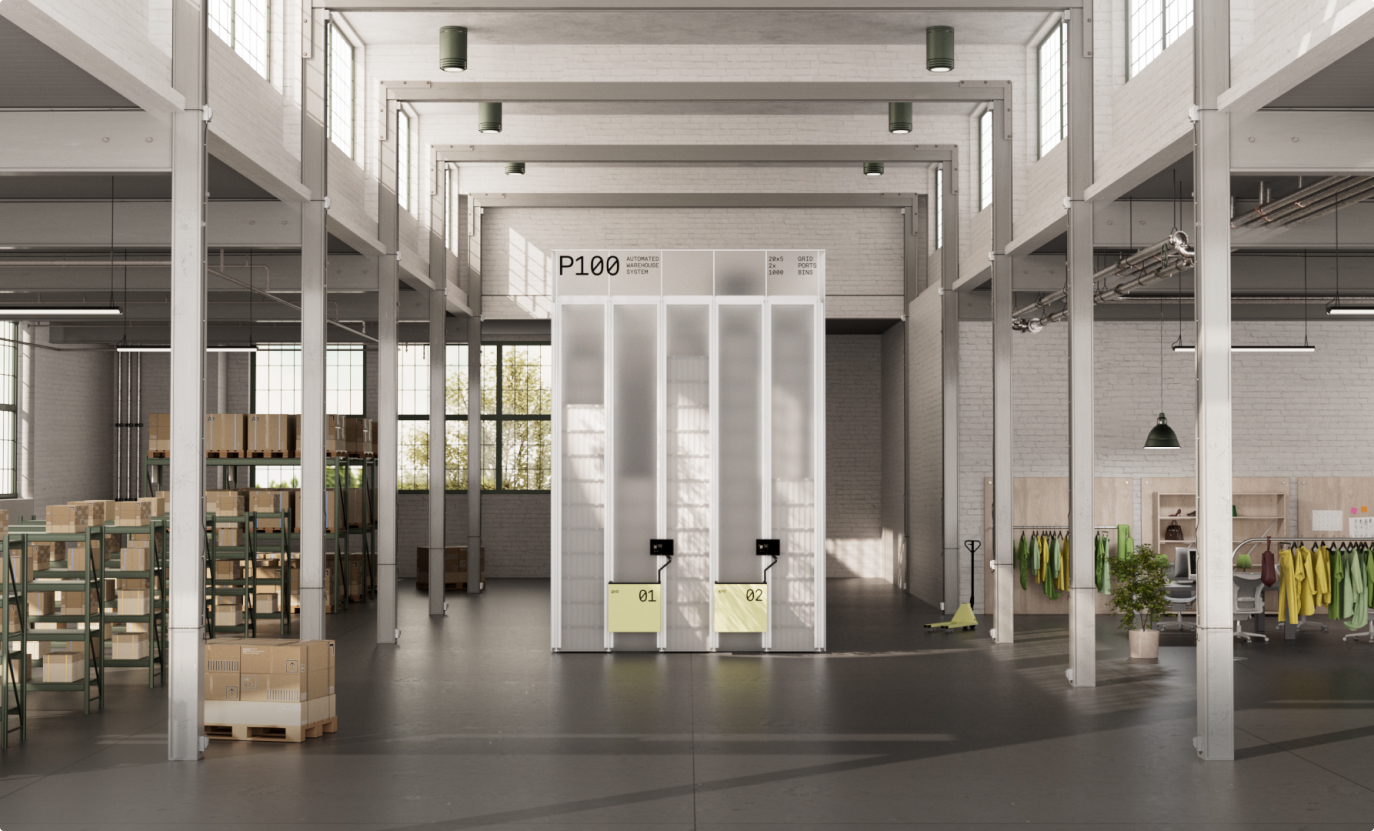