Scaling Without Breaking the Budget
Like many growing logistics providers, Souko started small—literally from a garage. Over the years, their success led them to a 40,000 sq. ft. warehouse, but their fulfillment process remained largely manual and inefficient.
Key Cost Challenges Before Automation:
- Labor-Intensive Picking: Peak season required up to 15 pickers on the floor, driving high labor costs and long hours.
- Storage Limitations: The warehouse was reaching its capacity, threatening future growth without expansion.
- Slow Picking Speeds: Workers averaged 60-80 lines per hour, making it difficult to keep up with demand.
- Order Errors: Picking mistakes led to returns, lost revenue, and inefficiencies.
“We had limitations around space and output. We could only store so much inventory, and we could only fulfill so many orders per day. That limited our growth,” said Connor MacArthur, founder of Souko.
Smarter Storage with Pio
Rather than adding more workers or expanding warehouse space, Souko optimized what they already had. By integrating Pio’s plug-and-play automation, they unlocked higher efficiency, faster fulfillment, and major cost savings.
“We needed automation that could bolt onto our existing operations without a massive overhaul. Pio fit the bill perfectly. The simplicity, cost-effectiveness, and space optimization were game-changers.”
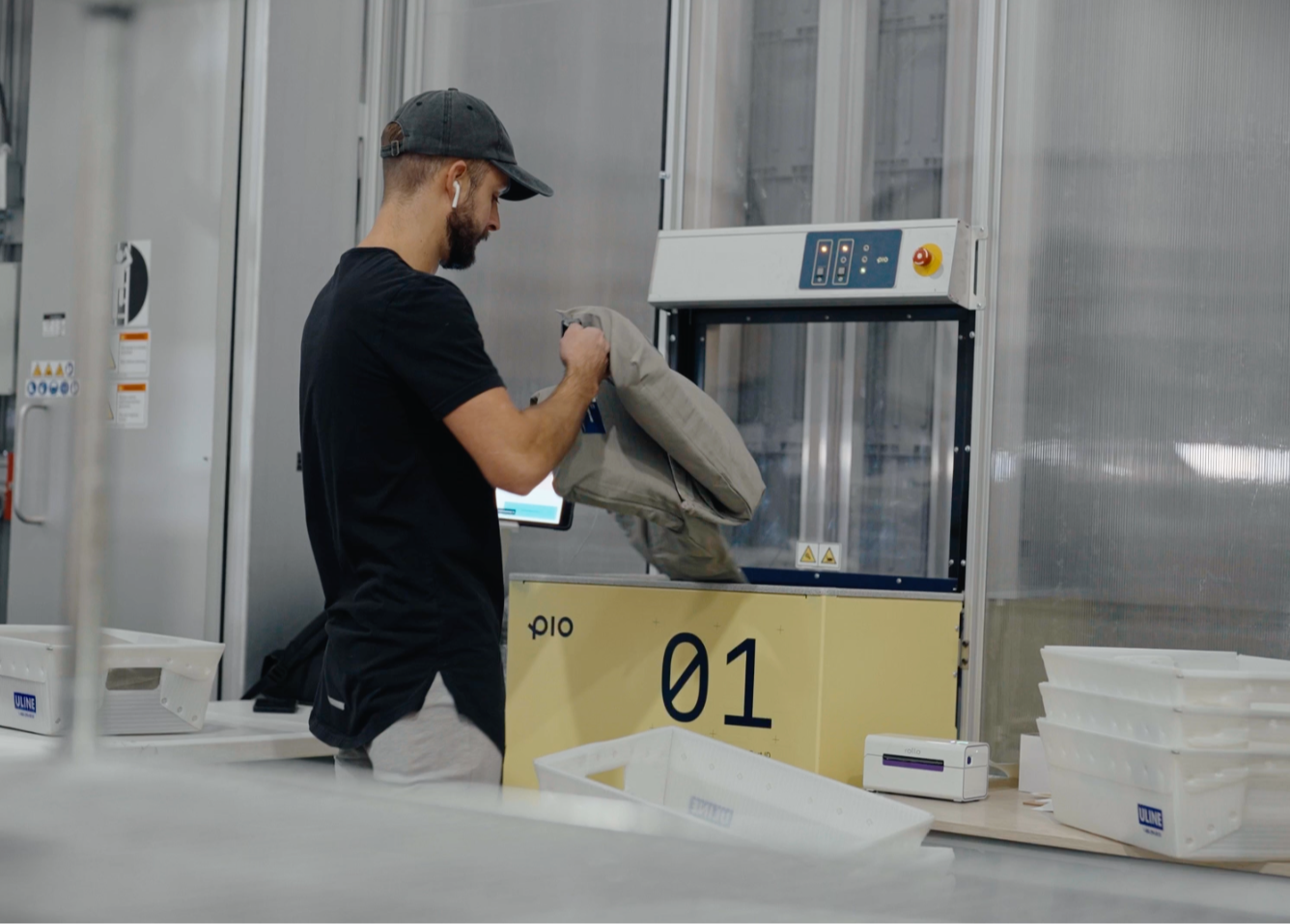
Saving Big Through Efficiency Gains
Labor Cost Savings: est. $241,920 per Year
By automating order picking, Souko cut its picking workforce in half. Instead of 15 pickers, they now fulfill the same volume with just 7-8 workers.
- Fewer workers, same output
- Lower payroll expenses
- Reduced seasonal labor needs
Estimated Annual Labor Savings:
$18/hour per worker × 8-hour shifts × 7 fewer workers = $1,008 saved per day
$1,008/day × 20 workdays per month = $20,160 saved per month
$20,160/month × 12 months = $241,920 saved per year
Note: Souko did not reduce headcount but reallocated staff to other operational roles. This figure represents potential labor cost savings that could be realized if headcount were reduced or hiring was minimized as a result of automation.
Space Optimization: $56,000–$96,000 Saved Annually
With Pio’s dense cube storage, Souko consolidated inventory within a much smaller footprint, freeing up thousands of square feet of warehouse space.
- Avoided costly warehouse expansion
- Reduced need for offsite storage or leasing additional space
In Salt Lake City, industrial space rents for $7–12 per sq. ft. annually. If Pio helped Souko free up even 2,000 sq. ft:
the savings amount tO...
$7–12 per sq. ft. × 2,000 sq. ft. = $14,000–$24,000 per year in avoided costs.
In reality, Souko has freed up at least 8,000 sq. ft, which means the actual savings total up to around four times higher:
$7–12 per sq. ft. × 8,000 sq. ft. = $56,000–$96,000 per year in avoided costs.
Tripled Order Processing Speeds
Picking speeds jumped from 60-80 lines per hour to 240-285, meaning fewer workers can process far more orders.
- More throughput without increasing headcount
- Faster fulfillment without employee burnout
- Increased accuracy (99.9%) reducing costly mis-picks and returns
“We’ve been able to grow without increasing our footprint or doubling our workforce. That alone has made a huge impact,” said Connor.
Scaling Smarter, Not Harder
By automating storage and fulfillment, Souko didn’t have to lease a bigger warehouse or hire more pickers to handle peak season. Instead, they scaled more profitably—cutting costs while increasing efficiency.
The Bottom Line?
-
Labor reduced by 50%, saving ~$240K annually
-
Storage optimized, saving up to $96K per year
-
Order picking speeds tripled, increasing throughput without added cost
With six-figure savings and long-term scalability, Souko is proving that automation isn’t just for the industry giants—it’s the key to growing efficiently while staying lean.
Is Your Warehouse Leaving Money on the Table?
Pio helps warehouses like Souko's save space, cut labor costs, and fulfill orders faster. If you’re ready to scale without breaking the budget, it’s time to see what smarter storage can do for you. Contact our team today.
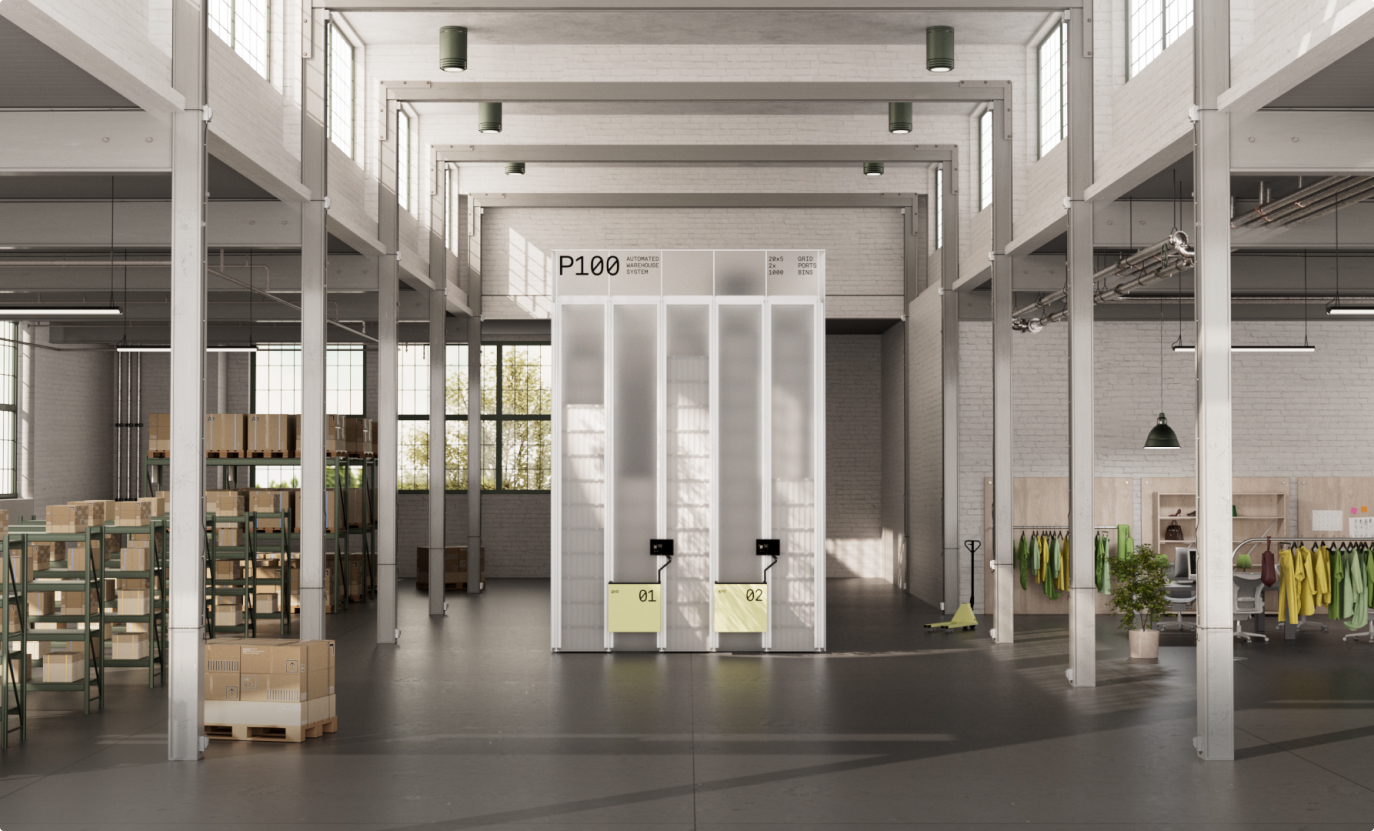